
“We decided to move forward with 42Q’s system for our Delaware plant because of its ability to be deployed quickly-we needed to have the solution up-and-running in six weeks and in production within three months-and its integration with our ERP system,” says Pradhan. Given its adaptability across verticals, scalable and rapid deployment capabilities, integration capabilities with Oracle, and flexible pricing model, 42Q appealed to Bloom Energy. Today, 42Q's solution is a fully featured, cloud-based, and multi-tenant MES global solution built on AWS," says Wellington Giolo, Senior Director of Business Development and Strategic Alliances at 42Q.
BLOOM ENERGY SOFTWARE
"As a business unit, we re-designed the internal software solution to make it fully cloud-ready. Given the success of the solution and its ability to meet a market niche for other manufacturers, Sanmina launched 42Q as a separate business unit and commercialized product. The company’s MES software was initially developed-and still used today-for internal manufacturing process tracking and management across the manufacturing plants of Sanmina, its parent company and an end-to-end solution provider across verticals for original equipment manufacturers (OEMs). Working with 42Q to Deploy a Cloud-Based MES System Across Three Unique Manufacturing Facilities We also needed a solution that could integrate directly with our backend Oracle ERP solution.” The company began evaluating new solutions and became familiar with 42Q.

"The software wasn't meeting our requirements, and we needed to find a solution we could deploy within our final assembly plant to coincide with its opening. "We first experimented with an on-premises system, and found it wasn’t the right solution," says Ajay Pradhan, Bloom Energy's Senior Director of IT Applications, Infrastructure, and Information Security. The company sought to better control its systems and data within the factory. As the company grew, it sought to replace a paper-based manufacturing operations data-capturing system at one of its greenfield manufacturing facilities in Delaware-focused on final assembly and repairs-with a more efficient and scalable manufacturing execution system (MES).

The company operates different plants in the United States that handle unique facets of the company’s manufacturing workflow and processes. Various moving pieces must come together for Bloom Energy to implement its technology and manufacture its hardware at scale. The company’s platform empowers customers to personalize their energy consumption for on-site power while reducing carbon emissions. Based on the company’s proprietary solid oxide fuel cell technology, Bloom Energy Servers convert fuel into electricity with high efficiency.
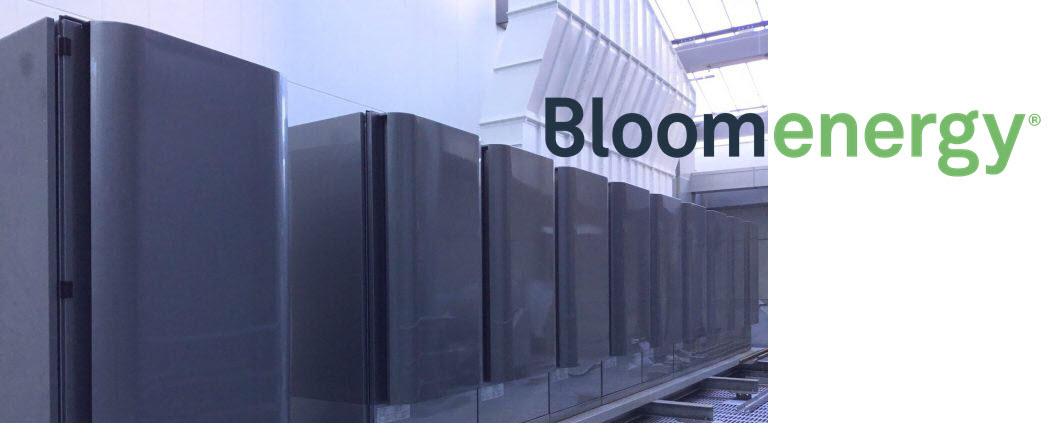
With a mission to make clean energy available to everyone in the world, Bloom Energy is at the forefront of innovation in the clean energy space.

And, 60 percent of Fortune 100 companies have set goals to increase the use of renewable energy in their operations. According to a Bloomberg New Energy Finance report, global markets saw three percent growth in clean energy investment, to $333.5 billion, in 2017. Embodiment methods may include determining an impedance of a set of fuel cells using electrochemical impedance spectroscopy, determining an ohmic polarization of the set of fuel cells from the impedance, determining a concentration polarization of the set of fuel cells from the impedance, comparing the ohmic polarization of the set of fuel cells to a first threshold, comparing the concentration polarization of the set of fuel cells to a second threshold, and initiating a corrective action when the ohmic polarization is above the first threshold or when the concentration polarization is below the second threshold.More and more companies across industries are investing in clean and sustainable energy solutions. Abstract: Systems, methods, and devices of the various embodiments provide a hardware and software architecture enabling electrochemical impedance spectroscopy (“EIS”) to be performed on multiple electrochemical devices, such as fuel cells, at the same time without human interaction with the electrochemical devices and to use EIS to dynamically monitor the performance of a fuel cell system.
